
Each chip may comprise an edge emitting semiconductor laser. The bars may then be cleaved or diced along a second dimensional axis (e.g., perpendicular to the first dimensional axis, but still in the plane of the surface of the wafer) to produce chips 106. A semiconductor wafer 102 is cleaved along a first dimensional axis (in the plane of the surface of the wafer) into bars 104. 1, a top level diagram of a chip singulation process, consistent with embodiments of the present disclosure, is shown and described. For example, (1,0,0) defines a plane that is perpendicular to the direction. Likewise, the term (x,y,z) indicates a plane in the x,y,z coordinate system. For example, defines a vector in the x-direction. It will be appreciated, however, that the processes and methods described herein for fabrication of laser chips may also be applied to the fabrication of other semiconductor devices and materials.Īs used herein, and consistent with standard crystallography nomenclature, the term indicates a direction vector in an x,y,z coordinate system. Additionally, improving the precision of the chip dimensions may facilitate hybrid integration of laser chips into photonic integrated circuits. The use of an etched V-groove to guide the cleave when singulating devices, as will be explained in greater detail below, may improve the throughput and yield of laser chip production. The etched trench may be formed as a V-shaped groove, to increase the precision of the cleave break, through the use of an etchant chemical that etches the semiconductor crystal planes of the wafer in a selective manner. Because the scribe line is formed by chemical etching, there may be less opportunity for mechanical damage and particle generation (e.g., contamination) in the process and the likelihood of chipping the laser during the cleaving process may be reduced. The improved scribing process may employ chemical etching to produce an etched trench on the wafer level which increases cleaving precision and reduces process time.

The fabrication of edge-emitting semiconductor lasers, consistent with embodiments described herein, generally includes the separation or singulation of a semiconductor wafer into individual chips (e.g., laser chips) using an improved scribing process to facilitate cleaving of the wafer along the scribe lines. 6 illustrates a scribe etch process consistent with an embodiment of the present disclosure. 5 illustrates a co-aligned scribe etch process consistent with an embodiment of the present disclosure.įIG. 4 illustrates a scribe etch process consistent with an embodiment of the present disclosure.įIG.
#Groove scribe website windows
3 illustrates an arrangement of scribe etch windows on a chip wafer consistent with an embodiment of the present disclosure.įIG. 2 presents cross sectional images of V-groove etch profiles consistent with an embodiment of the present disclosure.įIG. 1 is a top level diagram of a chip singulation process consistent with embodiments of the present disclosure.įIG. These and other features and advantages will be better understood by reading the following detailed description, taken together with the drawings wherein:įIG. What is needed, therefore, is an improved scribing process that avoids these issues.
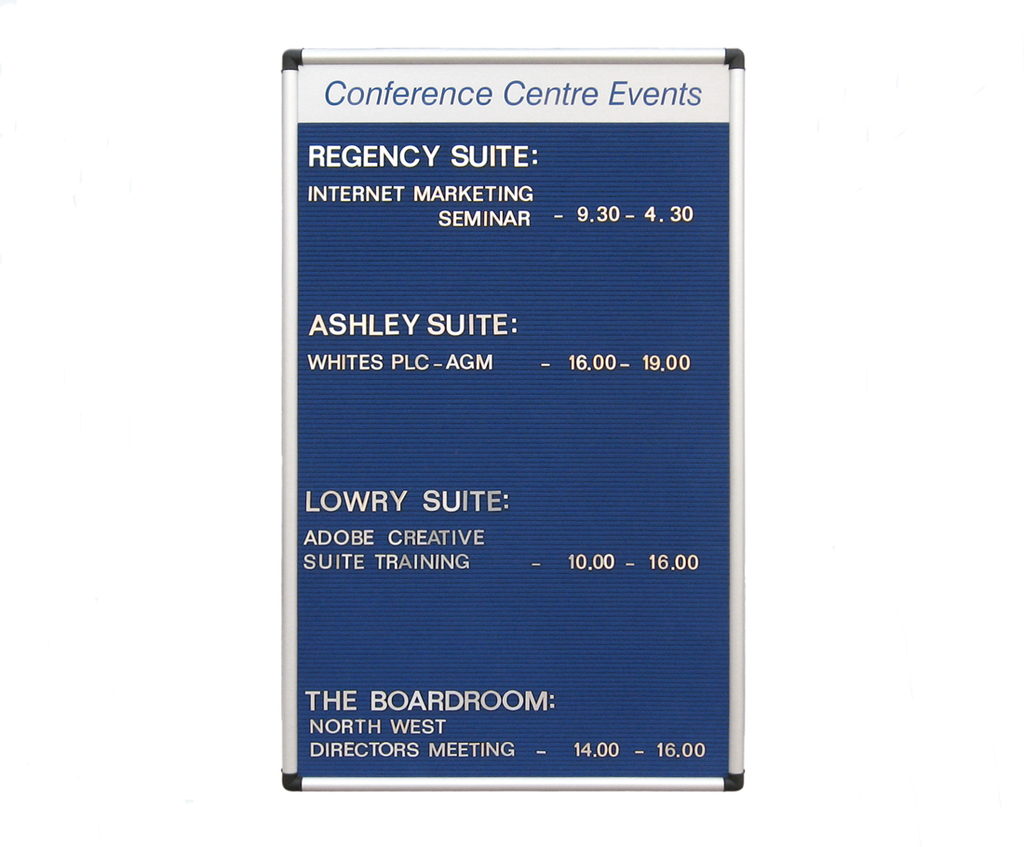
Additionally, coatings applied to the wafer or may interfere with the scribing process. Another problem is that the scribing process can create particles, damage, and chipping on the laser chip. Furthermore, the precision of the break is limited by the precision of the scribe mark. One problem is that the scribing requires relatively high precision tooling which is slow and expensive. There are, however, several problems with the current scribing process. The cleaving process generally involves the scribing of marks on a portion of the semiconductor wafer and then applying a force which causes the semiconductor to break along a crystal plane that is aligned with the scribe mark.
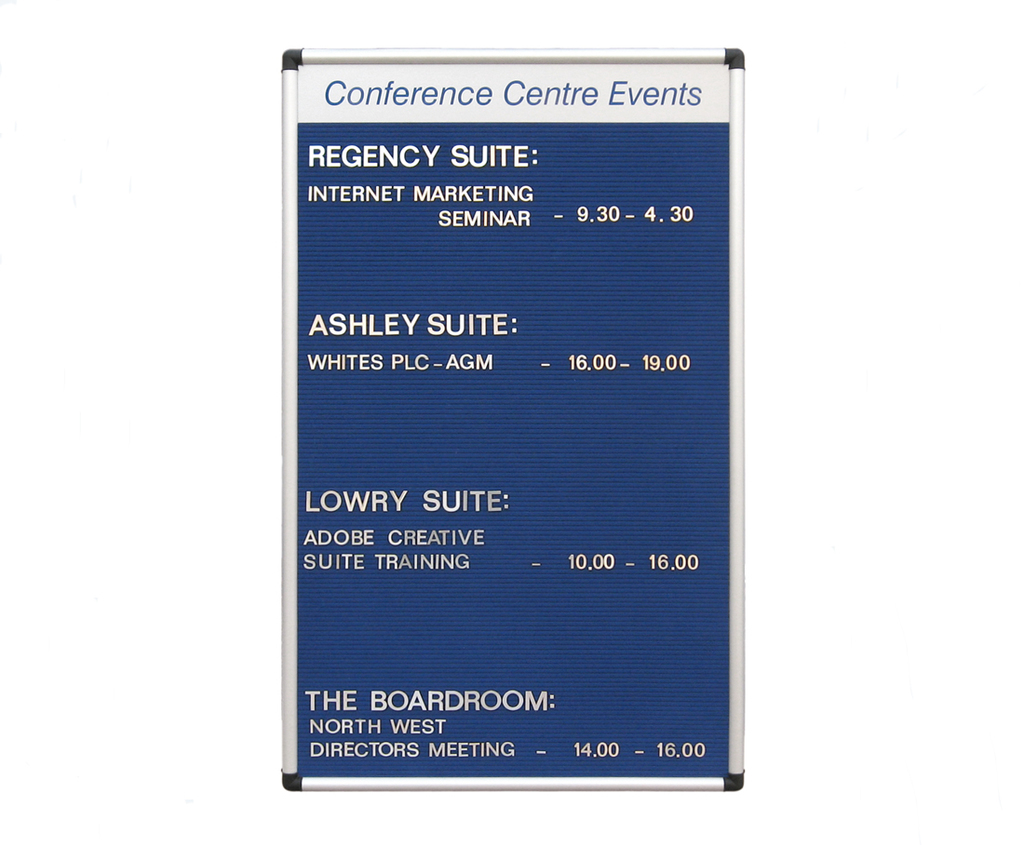
Due to the relatively small size of the chips and the fact that the quality of the chip edge is important for proper laser operation, cleaving has been a preferred process for the production of semiconductor laser chips. The separation process may typically be accomplished by sawing, laser cutting or cleaving the wafer. The fabrication of edge-emitting semiconductor lasers generally requires the separation of a semiconductor wafer into individual chips where, for example, each chip comprises a laser. The present disclosure relates to semiconductor laser chip manufacturing and more particularly, to an improved scribe etch process for semiconductor laser chip manufacturing.
